Get to Know More About Todays Manufacturing Industry
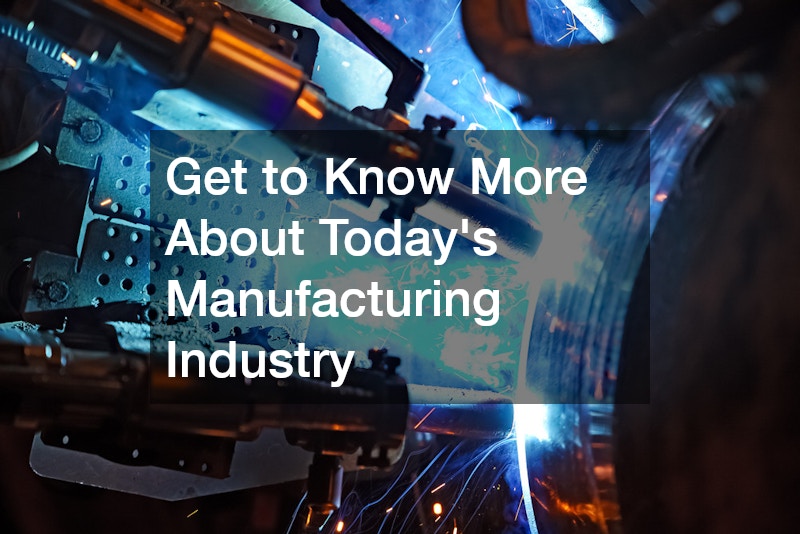
The manufacturing industry has undergone significant transformations in recent years, driven by advancements in technology, shifts in global supply chains, and evolving consumer demands. This dynamic sector is essential to the global economy, producing goods that range from everyday consumer products to specialized industrial equipment. In this comprehensive guide, we’ll explore the key aspects of today’s manufacturing industry, highlighting various processes, technologies, and sectors that are shaping its future.
The Evolution of Manufacturing: From Manual Labor to Automation
The manufacturing industry has come a long way from its origins in manual labor and handcrafted goods. The Industrial Revolution marked the beginning of mass production, with machinery replacing much of the manual work previously done by skilled artisans. Today, automation and robotics are at the forefront of manufacturing, driving efficiency, precision, and scalability.
Robotic Fabrication has revolutionized the manufacturing process, allowing for the production of complex parts and assemblies with high precision and consistency. Robots can work tirelessly without fatigue, reducing the likelihood of errors and increasing productivity. In industries where precision is paramount, such as aerospace or automotive manufacturing, robotic fabrication is indispensable. These advancements have not only improved the quality of products but have also reduced the time required to bring new products to market.
However, the transition to automation doesn’t mean the elimination of human workers. Instead, the role of the worker has evolved. Today, skilled workers are needed to program, maintain, and oversee these automated systems. Electricians, for example, play a crucial role in ensuring that these systems operate smoothly, handling everything from installation to troubleshooting and repair.
The Role of Bulk Metal Fabrication in Modern Manufacturing
Bulk metal fabrication is a cornerstone of the manufacturing industry, providing the essential components needed for a wide range of products and structures. From the frames of buildings to the bodies of vehicles, bulk metal fabrication involves the cutting, shaping, and assembling of metal materials into usable products.
This process is critical in industries such as construction, automotive, and aerospace, where strong, durable materials are required. For instance, a truck bed manufacturer relies heavily on bulk metal fabrication to produce sturdy and reliable truck beds that can withstand heavy loads and harsh conditions. The quality of these fabricated metal parts directly impacts the performance and safety of the final product.
The bulk metal fabrication process has also benefited from advances in technology. Modern fabrication facilities use computer-aided design (CAD) software and computer numerical control (CNC) machines to produce metal parts with high precision and efficiency. These technologies allow manufacturers to create complex designs that would be difficult or impossible to achieve with traditional fabrication methods.
The Importance of Local Manufacturing: Supporting Communities and Reducing Carbon Footprints
Local manufacturing plays a vital role in supporting communities and reducing the environmental impact of production. By producing goods closer to where they are consumed, local manufacturers can reduce the carbon footprint associated with shipping and logistics. Even for things like shipping containers for helicopters. Additionally, local manufacturing helps create jobs and stimulate economic growth within communities.
One sector where local manufacturing is particularly important is local cabinet manufacturing. This industry not only provides high-quality custom cabinets for homes and businesses but also supports local economies by sourcing materials and labor from within the community. Local cabinet manufacturers often have closer relationships with their customers, allowing them to provide personalized service and products that meet specific needs.
Local manufacturing also contributes to sustainability by reducing the need for long-distance transportation, which is a significant source of greenhouse gas emissions. By producing goods locally, manufacturers can minimize their environmental impact while also providing faster delivery times and better customer service.
The Integration of Advanced Technologies in Manufacturing
The integration of advanced technologies is one of the most significant trends shaping the manufacturing industry today. From artificial intelligence (AI) to the Internet of Things (IoT), these technologies are transforming how products are designed, produced, and maintained.
Robotic fabrication is just one example of how advanced technology is being used in manufacturing. Another critical area is the use of AI and machine learning to optimize production processes. These technologies can analyze vast amounts of data to identify inefficiencies, predict equipment failures, and recommend improvements. This data-driven approach allows manufacturers to make more informed decisions, leading to increased productivity and reduced costs.
IoT technology is also playing a significant role in manufacturing. By connecting machines and devices to the internet, manufacturers can monitor and control production processes in real-time. This connectivity allows for better coordination across the supply chain, as well as improved maintenance and repair of equipment. For example, IoT sensors can detect when a machine is operating outside of its normal parameters, triggering preventive maintenance before a failure occurs. This proactive approach helps avoid costly downtime and extends the life of manufacturing equipment.
Heavy machinery repair and maintenance have also seen improvements due to these technological advancements. With predictive maintenance powered by IoT and AI, manufacturers can anticipate when machinery will need servicing and perform maintenance before issues escalate, ensuring continuous production and reducing the likelihood of unexpected breakdowns.
The Role of Industrial Supply Chains in Manufacturing
The efficiency and effectiveness of industrial supply chains are critical to the success of manufacturing operations. These supply chains involve the sourcing, transportation, and storage of raw materials and components, as well as the distribution of finished products to customers. A well-managed supply chain ensures that materials are available when needed, production schedules are met, and products are delivered to customers on time.
In the manufacturing industry, industrial supply companies provide the raw materials, tools, and equipment needed to keep production lines running smoothly. These suppliers play a crucial role in maintaining the flow of goods through the supply chain, ensuring that manufacturers have access to the resources they need to meet demand.
Supply chain management has become increasingly complex in recent years, with manufacturers needing to navigate global supply networks, fluctuating demand, and the challenges of just-in-time production. Advanced software solutions and technologies like blockchain are being used to improve supply chain visibility, traceability, and efficiency. These tools allow manufacturers to track materials and products throughout the supply chain, identify potential bottlenecks, and respond quickly to disruptions.
The Impact of Globalization on Manufacturing
Globalization has had a profound impact on the manufacturing industry, both in terms of opportunities and challenges. On the one hand, globalization has opened up new markets for manufacturers, allowing them to reach customers around the world. On the other hand, it has also introduced increased competition, as manufacturers must now compete with companies from different countries with varying levels of production costs.
One of the most significant effects of globalization has been the outsourcing of manufacturing to countries with lower labor costs. This trend has led to the rise of global supply chains, where components are produced in different parts of the world and then assembled in another location. While this approach can reduce production costs, it also increases the complexity of supply chain management and can make manufacturers more vulnerable to disruptions, such as natural disasters or geopolitical tensions.
In response to these challenges, some manufacturers are exploring reshoring, or bringing production back to their home countries. This trend is driven by the desire to reduce supply chain risks, improve quality control, and support local economies. For example, a plastic preform supplier might choose to reshore production to reduce lead times and ensure consistent quality.
The Importance of Sustainability in Manufacturing
Sustainability has become a critical focus for manufacturers as they seek to reduce their environmental impact and meet the growing demand for eco-friendly products. From reducing energy consumption to minimizing waste, manufacturers are implementing a range of strategies to improve their sustainability performance.
One area where sustainability is particularly important is in the use of materials. Manufacturers are increasingly looking for ways to reduce their reliance on non-renewable resources and incorporate more sustainable materials into their products. For example, bulk metal fabrication companies are exploring the use of recycled metals, which require less energy to produce and help reduce the environmental impact of mining and processing raw materials.
Energy efficiency is another key focus for sustainable manufacturing. By optimizing production processes and investing in energy-efficient equipment, manufacturers can reduce their energy consumption and lower their carbon footprint. This approach not only benefits the environment but also leads to cost savings, as energy is often one of the most significant expenses for manufacturers.
Waste reduction is also a critical aspect of sustainability in manufacturing. Manufacturers are implementing strategies to minimize waste throughout the production process, from reducing material waste during fabrication to recycling and reusing by-products. For example, local cabinet manufacturing companies might implement practices that optimize the use of wood materials, reducing scrap and utilizing leftover pieces in other products.
The Role of Custom Manufacturing in Meeting Diverse Market Needs
As consumer preferences become more diverse, the demand for custom and personalized products has grown. Custom manufacturing allows companies to produce products tailored to the specific needs and preferences of their customers, providing a competitive advantage in the marketplace.
Custom manufacturing is particularly prevalent in industries such as automotive, aerospace, and consumer goods, where products often need to meet specific performance requirements or aesthetic preferences. For example, a truck bed manufacturer might offer custom truck beds designed to meet the unique needs of different industries, such as construction, agriculture, or logistics.
The rise of digital manufacturing technologies, such as 3D printing and CNC machining, has made custom manufacturing more accessible and cost-effective. These technologies allow manufacturers to produce small batches of custom products without the need for expensive tooling or molds. This flexibility enables manufacturers to respond quickly to changing market demands and offer a wider range of products to their customers.
The Growing Importance of Industrial Cleaning in Manufacturing
Industrial cleaning is a critical aspect of maintaining a safe and efficient manufacturing environment. Clean facilities and equipment not only ensure the quality of products but also protect the health and safety of workers. In industries such as food and beverage, pharmaceuticals, and electronics, where contamination can have serious consequences, industrial cleaning is especially important.
Manufacturers rely on specialized industrial cleaning services to maintain the cleanliness of their facilities, including production lines, machinery, and workspaces. These services often involve the use of advanced cleaning technologies and techniques, such as high-pressure washing, steam cleaning, and chemical disinfection.
Regular industrial cleaning also plays a role in preventive maintenance by removing dirt, debris, and contaminants that can cause equipment to malfunction or wear out prematurely. For example, in heavy machinery repair and maintenance, keeping machinery clean is essential to prevent buildup that can lead to mechanical failures or reduce the efficiency of the equipment.
The growing focus on sustainability has also influenced the industrial cleaning industry, with many manufacturers seeking eco-friendly cleaning solutions that minimize the use of harmful chemicals and reduce water and energy consumption. Green cleaning products and techniques not only help protect the environment but also create a healthier workplace for employees.
The Role of Safety and Compliance in Manufacturing
Safety and compliance are fundamental to the success of any manufacturing operation. Manufacturers must adhere to a wide range of regulations and standards designed to protect workers, consumers, and the environment. Compliance with these regulations is not only a legal requirement but also a key factor in maintaining a company’s reputation and avoiding costly fines or legal actions.
One area where safety and compliance are particularly critical is in the use of hazardous materials. Manufacturers that work with chemicals, flammable materials, or other hazardous substances must implement strict safety protocols to prevent accidents and protect workers. This includes providing proper training, using protective equipment, and ensuring that facilities are designed and maintained to minimize risks.
In addition to safety, manufacturers must also comply with environmental regulations that govern emissions, waste disposal, and resource use. These regulations vary by country and industry, but they often require manufacturers to implement measures to reduce their environmental impact. For example, a plastic preform supplier might need to comply with regulations regarding the use and disposal of plastics, including recycling requirements and restrictions on certain types of plastic materials.
Compliance with quality standards is another critical aspect of manufacturing. Many industries have established standards, such as ISO certifications, that set the benchmarks for product quality and consistency. Adhering to these standards is essential for manufacturers that want to maintain a competitive edge and meet the expectations of their customers.
The Future of Manufacturing: Emerging Trends and Technologies
The manufacturing industry is constantly evolving, with new trends and technologies shaping the future of production. Some of the key trends that are expected to have a significant impact on the industry include:
Additive Manufacturing (3D Printing): Additive manufacturing, or 3D printing, is revolutionizing the way products are designed and produced. This technology allows manufacturers to create complex parts and prototypes quickly and cost-effectively, without the need for traditional tooling. 3D printing is particularly useful for producing small batches of custom products or for creating intricate designs that would be difficult to achieve with traditional manufacturing methods.
Smart Manufacturing and Industry 4.0: The concept of Industry 4.0 refers to the integration of digital technologies, such as IoT, AI, and big data, into the manufacturing process. Smart manufacturing uses these technologies to create more connected, automated, and data-driven production environments. This approach enables manufacturers to optimize production, improve quality, and reduce costs by making real-time adjustments based on data insights.
Sustainable Manufacturing: As environmental concerns continue to rise, sustainable manufacturing practices are becoming increasingly important. Manufacturers are adopting greener processes, materials, and energy sources to reduce their environmental impact and meet the growing demand for eco-friendly products. This trend is expected to continue, with more manufacturers seeking to minimize waste, reduce emissions, and conserve resources.
Reshoring and Localization: The COVID-19 pandemic highlighted the vulnerabilities of global supply chains, leading to a renewed interest in reshoring and localization. Manufacturers are increasingly looking to produce goods closer to their customers to reduce supply chain risks, improve lead times, and support local economies. This trend is expected to drive growth in local manufacturing sectors and encourage the development of more resilient and flexible supply chains.
Collaborative Robots (Cobots): Collaborative robots, or cobots, are designed to work alongside human workers, enhancing productivity and safety. Unlike traditional industrial robots, which are often isolated from workers due to safety concerns, cobots are equipped with advanced sensors and safety features that allow them to operate in close proximity to humans. Cobots are particularly useful in tasks that require precision, repetition, or heavy lifting, making them an ideal addition to manufacturing environments.
Advanced Materials: The development of new materials, such as composites, nanomaterials, and biomaterials, is opening up new possibilities for manufacturing. These materials offer improved performance, durability, and sustainability compared to traditional materials, making them attractive for a wide range of applications. For example, lightweight composites are being used in aerospace and automotive manufacturing to reduce weight and improve fuel efficiency, while biomaterials are finding applications in medical devices and packaging.
The Importance of Skilled Labor in Manufacturing
Despite the increasing automation of manufacturing processes, skilled labor remains a critical component of the industry. Skilled workers are needed to operate, maintain, and repair complex machinery, as well as to design and oversee production processes. The demand for skilled labor is expected to grow as manufacturers continue to adopt advanced technologies and expand their operations.
Electricians, for example, play a vital role in the manufacturing industry, ensuring that electrical systems are installed, maintained, and repaired to keep production lines running smoothly. Similarly, machinists, welders, and technicians are essential for operating and maintaining the equipment used in various manufacturing processes.
To meet the demand for skilled labor, many manufacturers are investing in workforce development programs, apprenticeships, and partnerships with educational institutions. These initiatives are designed to attract new talent to the industry and provide workers with the skills and knowledge they need to succeed in a rapidly changing manufacturing environment.
As the industry continues to evolve, the role of suppliers, skilled labor, and advanced technologies will become increasingly important in driving innovation and growth. By staying informed about the latest developments and adapting to the changing landscape, manufacturers can position themselves for success in the years to come.
Whether you’re involved in bulk metal fabrication, local cabinet manufacturing, or heavy machinery repair and maintenance, understanding the key trends and challenges in today’s manufacturing industry is essential for staying competitive and achieving long-term success. The future of manufacturing is bright, with endless opportunities for those who are willing to embrace change and continue to innovate.